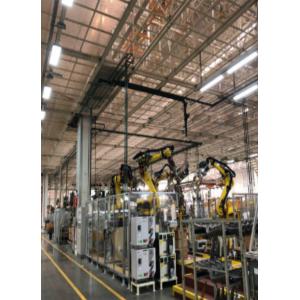
Add to Cart
High-end and pure electric light truck construction project UBS01 station of wide body welding line
1. Project name
High-end and pure electric light truck construction project UBS01 station automation transformation project of wide body welding line
2. Project time
2018.10
3. Project introduction
Models: 6 models collinear
Capacity: 35JPH
Robot: FANUC
Quantity: 30 units
Main line conveying method: reciprocating rod (SHUTTLE line)
4. Core technology
1. Flexible production line for six models
2. High-tempo and line-body models adopt sliding table switching
3. The line body automation rate is 98%
As far as each welding line is concerned, it is composed of welding process, transmission device, welding equipment (welding torch, welding robot); as far as the entire automobile body welding line is concerned, it generally includes the body side wall assembly line, body door Cover assembly line, floor assembly line, body welding main line, etc. (there is no absolute summary yet). Each part has corresponding main lines, sub-lines, left and right symmetrical lines and independent islands. According to the different production tempo, degree of automation and production methods, each line is divided into several stations: each station is connected as a whole through a transmission device, and each station is responsible for completing a part of the work.
Accompanying trolley through production line
The typical form of this production line is shown in Figure 4. It generally adopts the same trolley-type fixtures in different quantities, and is driven by a chain to a predetermined station. After manual feeding and manual welding, each car body is placed on the same fixture and different working stations. Complete the assembly. This form of production line has low production efficiency, high labor intensity, single-species special-line production, and the accuracy and quality of products are not easy to guarantee. It is a commonly used production form in the early days and is generally suitable for small batch production.
Buffer locking device
A total of 4 buffer locking devices are installed in the welding line transmission device, which are respectively distributed at both ends of the jacking frame, mainly to buffer and lock the horizontal movement of the "moving slide". The specific process is: when the "moving slide" is about to move to the end of the transmission device, it contacts with the buffer to slow down the movement speed: when the "moving slide" moves to the end of the transmission device, the travel switch commands the cylinder to clamp and fix on the moving The limit block on the slide plate thus plays a locking role. The device realizes the slow start and slow stop movement requirements of the transmission device of the automobile welding line, and ensures the safe and reliable operation of the transmission device.